Rotary screen printing is a traditional textile printing method that is widely used in printed textiles. It is ideal for printing on fabric, garments, and other substrates. This screen printing technique uses a rotating cylindrical screen to apply ink or dye onto materials.
It offers an efficient and versatile method of printing fabrics, producing vibrant designs with impressive durability. In this article, we will delve into the working process of rotary screen printing, its advantages, disadvantages, applications, and the future of rotary screen printing.
How Rotary Screen Printing Works
In rotary screen printing, the design to be printed is engraved or etched directly onto the surface of a thin nickel or steel mesh cylinder. This cylindrical screen continually rotates as the substrate passes underneath it. Ink is flooded onto the inside of the rotating screen. A rubber squeegee or roller presses the screen down onto the material being printed. As the screen rotates, ink is forced through the porous areas of the mesh onto the substrate.
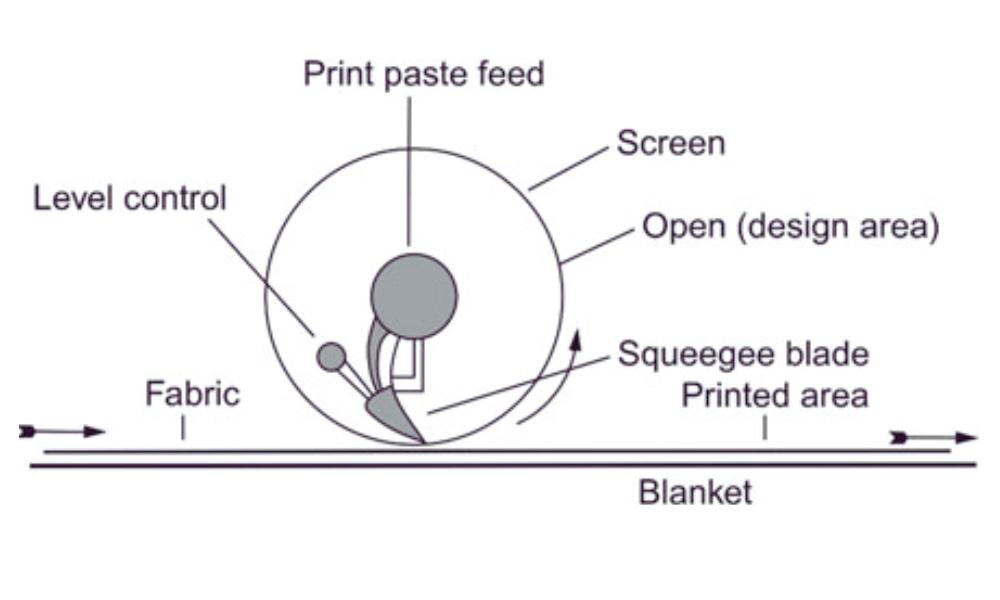
The basic components of a rotary screen printing machine include:
Cylindrical Screen – The rotating screen engraved with the image to be printed.
Squeegee – Located inside the screen, this rubber blade forces ink through the pores of the mesh.
Ink System – Controls the ink flood and regulates viscosity and temperature.
Print Table – The moving conveyor belt that passes the substrate underneath the rotating screen.
Rotary Screen Printing Process Flow
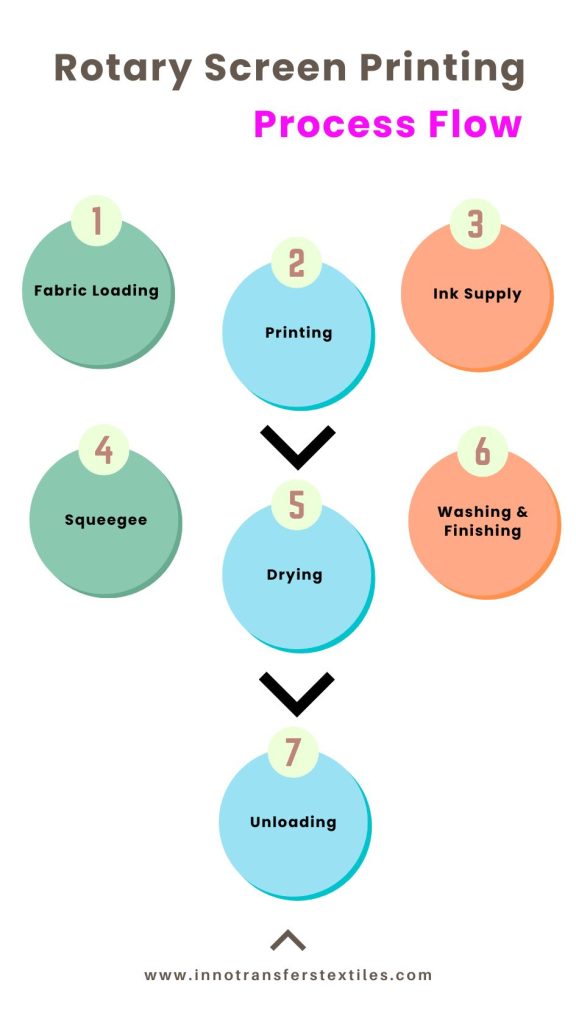
1. Fabric Loading – The fabric to be printed is loaded onto the feeder rollers and tensioned. This allows consistent movement through the printer.
2. Printing – The fabric passes underneath the rotating cylindrical screens. Each screen applies a different color. The screens turn continuously as the fabric moves.
3. Ink Supply – Inside the screens, ink or paste is pumped and flooded across the internal surface area.
4. Squeegee – A rubber squeegee blade located inside the screen squeezes the printing paste through the open mesh onto the fabric.
5. Drying – The printed fabric is fed into the drying oven to cure and set the inks. The heat from the oven evaporates any moisture in the paste.
6. Washing/Finishing – After drying, the fabric goes through washing stations to remove any excess paste. Additional finishing steps may be applied.
7. Unloading- Finally, the printed fabric is unloaded and rolled for further processing or shipment.
Advantages of Rotary Screen Printing
There are many benefits that make rotary screen printing popular across various industries:
High Print Speeds – Rotary screen printing is exceptionally fast and efficient, making it ideal for large production volumes. The continuous printing process enables higher output rates compared to traditional flatbed printing methods.
Repeatability – The printing cylinder allows for continuous repeat prints with no gaps or overlaps.
High Ink Density – The squeegee applies thick ink deposits, allowing for bright solid colors.
Versatility – This method can be used to print on a wide range of textile materials, including cotton, silk, polyester, and blends. It accommodates various fabric thicknesses and can handle intricate patterns with ease.
Cost Effectiveness – High production with low labor requirements results in very economical printing costs. Due to its efficient ink transfer process, rotary screen printing consumes less ink compared to other printing techniques, reducing operational costs.
Disadvantages of Rotary Screen Printing
Initial Setup Cost – The initial investment in rotary screen printing equipment and technology can be substantial. Small businesses and startups may find it challenging to bear these upfront costs.
Limited Resolution – Rotary screen printing may not achieve the same level of detail and resolution as some digital printing methods. Complex designs with fine lines and small elements might not be rendered as accurately.
Not Suitable for Small Orders – Due to its high-speed nature and setup requirements, rotary screen printing is better suited for large production runs. It may not be cost-effective for small-scale or custom orders.
Rotary Screen Printing Applications
Rotary screen printing is used across a diverse range of industries to print onto fabrics, garments, packaging, ceramics, and more.
Garment Printing
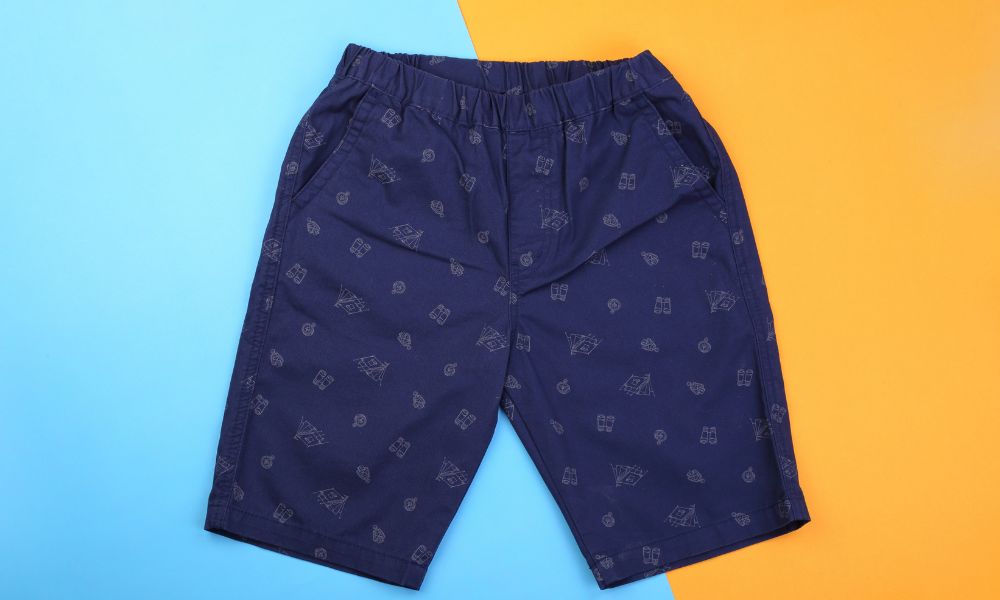
The garment industry widely uses rotary screen printing to decorate t-shirts, jerseys, polos, caps, bags, and other apparel items. It allows high-speed printing with photographic quality. Some common garment printing applications include:
T-Shirt Printing – Rotary printing is ideal for printing designs, graphics, logos, or text onto cotton t-shirts. It can print exact PANTONE colors with thick ink deposits.
Sports Uniforms – Nylon athletic jerseys for sports teams are frequently printed using the rotary method. It provides vibrant team logos and names.
Caps – Rotary printers print onto the front panel and sides of baseball caps and snapbacks. Prints withstand repeated washing and usage.
Tote Bags – Large area prints like patterns, photographs, and backgrounds can be printed onto canvas and cotton tote bags.
Sweatshirts & Jackets – High ink opacity allows rotary printing of hoodies, crewnecks, and jackets in both polyester and natural fabrics.
Textile Printing
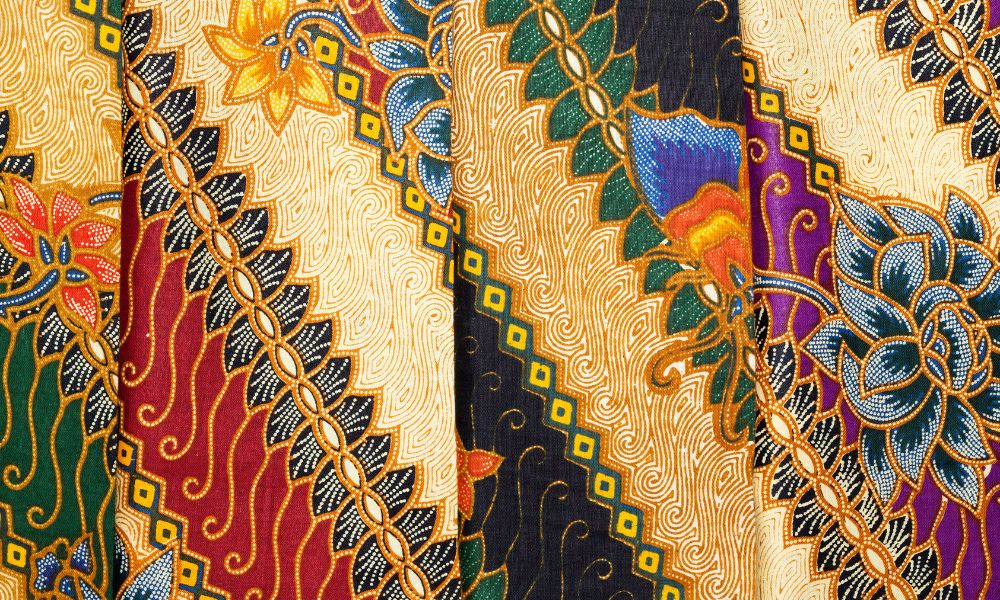
Decorating curtains, upholstery, towels, blankets, and other interior textiles with colorful patterns is made simple using rotary printing. Key applications are:
Upholstery Fabric – Rotary printing creates beautiful finished upholstery fabric for sofas, ottomans, and chairs using reactive or pigment inks.
Towels – Vibrant repeating patterns are printed onto cotton towels for decorative and promotional use.
Flags & Banners – Dye sublimation rotary printing produces weather-resistant graphics on nylon and polyester flags.
Bedding – Detailed imagery and custom designs can be printed onto curtains, duvet covers, sheets, and pillowcases.
The Future of Rotary Screen Printing
Rotary screen printing continues to evolve with technological improvements in inks, screens, and automation. Some innovations in this field include:
- High-resolution screens allow for more detailed prints.
- Inline pretreatment and curing stations for efficient workflows.
- Specialty inks like metallic, glow-in-the-dark, high density, and 3D effects.
- Digital file preparation allows quick design changes and reprints.
- Automated screen cleaning and recycling systems minimize downtime.
As technology progresses, rotary screen printing machinery is becoming more sophisticated, versatile, and efficient. The rotary method will continue to play an important role across printing industries worldwide.
Conclusion
Rotary screen printing has revolutionized the textile printing industry with its speed, efficiency, and versatility. From apparel to home furnishings, this printing method continues to leave its mark on various applications. Despite its limitations, ongoing efforts toward sustainable printing and technological advancements ensure that rotary screen printing remains a crucial player in the world of fabric printing.
FAQs
Is rotary screen printing suitable for intricate designs on fabrics?
While rotary screen printing can handle detailed designs, it may not match the resolution achieved by digital printing methods for extremely intricate patterns.
Can rotary screen printing be used on non-textile materials?
Rotary screen printing is primarily designed for textiles; however, it may find limited application in printing on certain non-textile materials.
How long does it take for the prints to dry after rotary screen printing?
The drying time depends on the ink type, fabric, and environmental conditions. In most cases, prints dry within a few minutes to a couple of hours.
Is rotary screen printing more cost-effective than digital printing for large orders?
Yes, rotary screen printing is generally more cost effective for large production runs, especially when consistent designs are required.
Thank you for sharing insights into your rotary display screen printing process. Your dedication to fantastic is evident in every print. Great read!
Your website is very inspiring with high-quality content. We are sure that you will find additional useful information on our website. Come on, visit us at Konveksi Seragam Kerja and we can collaborate with each other.
Warm Regard.
Thanks for your valuable comments.