Introduction to Digital Printing on Textiles
Digital printing has revolutionized the textile industry by offering endless possibilities for vibrant and detailed designs on various fabric materials. Digital printing on textiles refers to the process of using inkjet technology to transfer digital designs onto fabric surfaces.
Basically, it takes images straight from your computer and puts them onto all sorts of things – paper, fabric, plastic, and more. Unlike traditional printing methods, which involve screens or plates, digital printing enables direct printing from a digital file onto the fabric. This technique allows for greater design flexibility and customization, making it a popular choice for designers and manufacturers.
How Digital Printing Works on Textiles
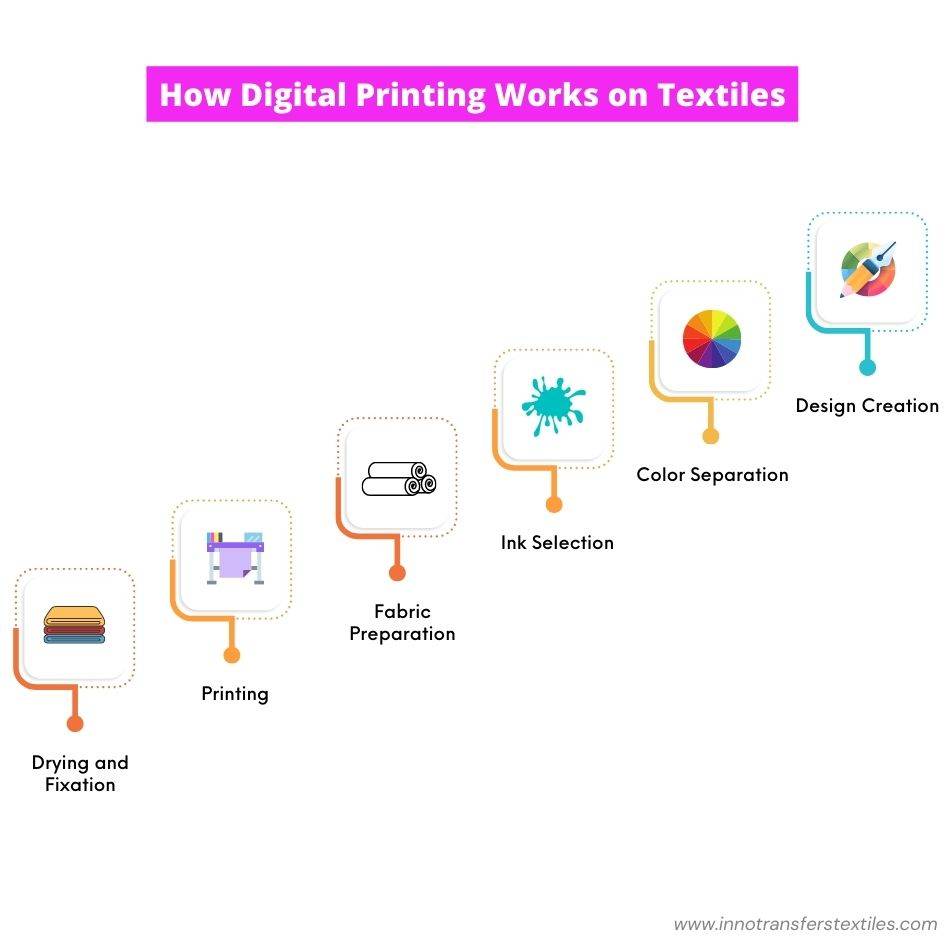
Design Creation
The process begins with creating a digital design using graphic design software like (Adobe Illustrator) and the CMYK color model is used as the basic color. Designers can unleash their creativity and develop intricate patterns, vibrant colors, and detailed imagery. The design can be custom-made or selected from a range of existing patterns.
Color Separation
Once the design is ready, it is separated into individual color channels. This step is crucial for digital printing as it allows the printer to apply each color separately during the printing process. By separating the colors, the printer can achieve accurate color reproduction and ensure that each shade stands out distinctly.
Ink Selection
Choosing the right ink is essential for achieving the desired color vibrancy and durability on the fabric. Different types of inks are available for digital textile printing, including reactive, acid, sublimation, pigment, and disperse inks. The selection of ink depends on the fabric type, desired color gamut, and intended application of the printed fabric.
Ink Characteristics of Digital Textile Printing
Ink | Fabric Type | Pre-treatment | Post-treatment |
Pigment | Natural, Synthetic | No (Usually) | Dry heat |
Acid | Wool, silk, Nylon | Yes | Steam heat |
Reactive | Cotton, Rayon, Silk | Yes | Steam heat |
Disperse Dye | Polyester | yes | Steam or dry heat |
Disperse sublimation | Polyester | No | Dry heat transfer |
Fabric Preparation
Before printing, the fabric needs to be prepared to receive the ink. This involves cleaning and treating the fabric to remove any impurities or finishes that may hinder ink absorption. Fabric preparation ensures optimal print results and enhances the longevity of the print.
Printing
Once the design is finalized and the fabric is prepared, the printing process can commence. In digital textile printing, the design is digitally transferred from the computer onto the fabric using specialized printers. These printers use advanced inkjet technology to deposit the ink onto the fabric in precise patterns, replicating the desired design. The printing can be done using either a direct-to-fabric method or a transfer paper method, depending on the specific printer and ink being used.
Drying and Fixation
After the ink is applied to the fabric, it needs to be dried and fixed to ensure its permanence and resistance to fading or washing. Drying can be done through various methods such as air drying, heat drying, or a combination of both. Fixation, on the other hand, typically involves applying heat and pressure to the printed fabric, which helps the ink bond with the fibers and ensures colorfastness and durability.
Process Flowchart for Digital Textile Printing
From design files to vibrant fabrics, digital printing unfolds in a dynamic dance of precision and technology. Raw canvas journeys through meticulous steps – treated, printed, steamed, stretched, dried, and finished – each stage seamlessly feeding into the next. The continuous process flow chart for digital printing is described below:
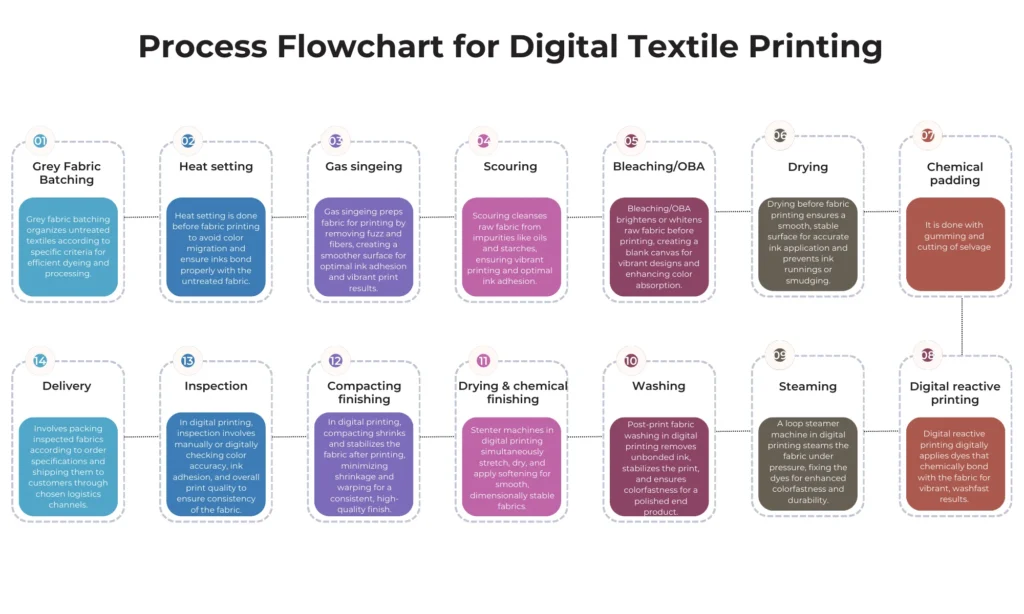
Digital Printing on Different Types of Fabrics
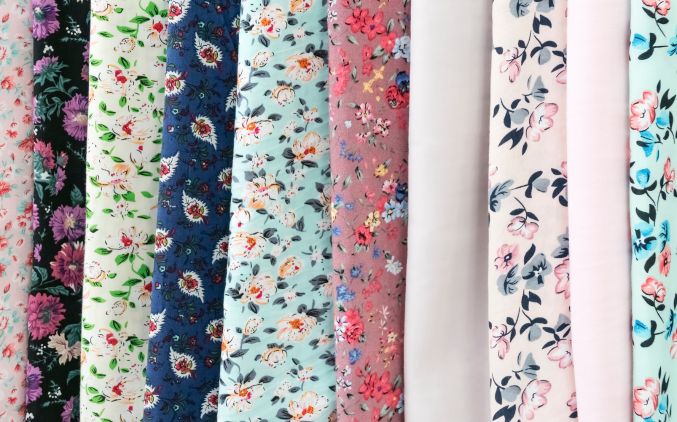
Digital Printing Fabrics with Reactive Inks
For natural fibers including cotton, rayon/viscose, silk, bamboo, and hemp, reactive inks are utilized. However, it is not appropriate for synthetic and polymeric fibers.
A chemical reaction occurs during the entire process, which includes correct pre-treatment, printing, and high-temperature steaming, causing the dye to combine and permanently lock the color in the fibers.
To get rid of any leftover ink, the fabric is washed after being steamed and softened. Bright colors and durable prints with excellent wash and rub fastness are the end results.
Digital Printing Fabrics with Pigment
One of the most flexible types of digital textile printing is pigment fabric printing. Both synthetic and natural fibers can be treated with it. You may print on 100% polyester, cotton-poly mixes, silk, rayon, and cotton using pigment inks.
The way pigment and reactive printing vary from one another is that in pigment printing, colors are “placed” on the fabric’s surface using adhesive, preventing the ink from penetrating the fibers.
Following the pigment ink printing process, the cloth is heated in a dry heating machine to solidify the color on the fabric’s surface by heating the glue included in the pigment inks.
Pigment printing is a far more environmentally friendly method than any other method because it requires less water and energy, and uses inks that last longer.
Digital Printing Fabrics with Acid Inks
Acid ink printing is a great way to color many fabrics. It works well on natural materials like wool and silk, which are hard to dye, and also on synthetic materials like nylon. This method creates bright colors that soak all the way through the fabric. It’s especially useful for fabrics that stretch and need to stay colorful even in chlorine or saltwater.
While similar to a different technique (reactive printing), acid ink printing involves extra steps. First, the fabric needs special treatment to make the design clear and the color last. Then, after printing, the fabric needs steaming in a special machine for nearly an hour. Finally, it needs washing to remove any leftover ink or treatment chemicals.
Although acid ink printing takes time and special equipment, it’s the best choice for getting beautiful, long-lasting colors on delicate fabrics or fabrics for tough conditions.
Digital Printing Fabrics with Acid Inks Sublimation or Dye-Sublimation
This cutting-edge technique works best on materials like polyester and spandex, but it won’t work on natural fibers like cotton or silk.
Here’s the magic behind it: the dye skips the liquid stage entirely, transforming from solid to gas and bonding directly with the fabric’s fibers.
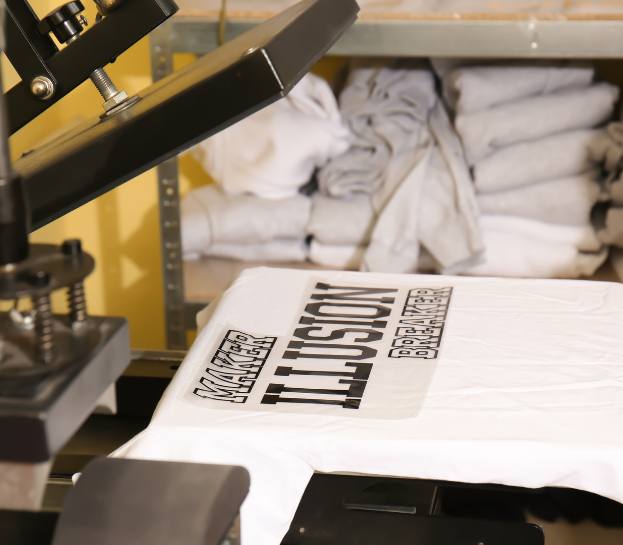
First, a special transfer paper gets printed with eco-friendly inks you can look further on choosing the best transfer paper for your project. Then, a heat press comes into play. Under high heat, the ink turns into gas, sinks into the fibers, and creates a permanent, fade-resistant design. The best part? The fabric stays soft and comfortable!
Advantages of Digital Printing on Textiles
Digital printing on textiles offers several advantages over traditional printing methods:
Design Flexibility: Digital printing allows for unlimited design possibilities, including intricate patterns, gradients, and photographic details. Digital textile printing (DTP) system can supposedly produce 16 million colors and shades. Hence, changes can be made easily without incurring additional setup costs.
Cost-effectiveness: Digital printing eliminates the need for costly screens or plates, making it a more affordable option for small production runs or customized orders. It also reduces waste as it requires fewer materials and resources.
Quick Turnaround: The digital printing process is faster compared to traditional methods, enabling shorter production lead times. This is especially beneficial for time-sensitive projects or fast-changing fashion trends.
High Print Quality: Digital printing offers exceptional print resolution and color accuracy, resulting in sharp and vibrant designs. It can reproduce intricate details and complex color gradients with precision.
Last but not least, Digital printing on textiles is an environmentally friendly alternative to conventional printing methods, addressing the pollution issues prevalent in the textile industry. This advanced technology not only reduces water consumption but also minimizes pollution by eliminating the discharge of dyes and chemicals. Furthermore, as an additional eco-friendly option, you can choose our Innotransfers, for high-quality heat transfer textile printing. Innotransfer offers a sustainable approach to printing by using eco-friendly processes.
Applications of Digital Printing in Fashion Industry
Digital printing has transformed the fashion industry by allowing designers to create unique and personalized garments. Some common applications include:
Customized Apparel: Customized apparel refers to clothing items that are tailored or personalized according to individual preferences, measurements, or design choices. Digital printing enables the production of customized clothing items, such as t-shirts, dresses, and activewear. Customers can have their own designs printed or choose from a wide range of pre-designed patterns.
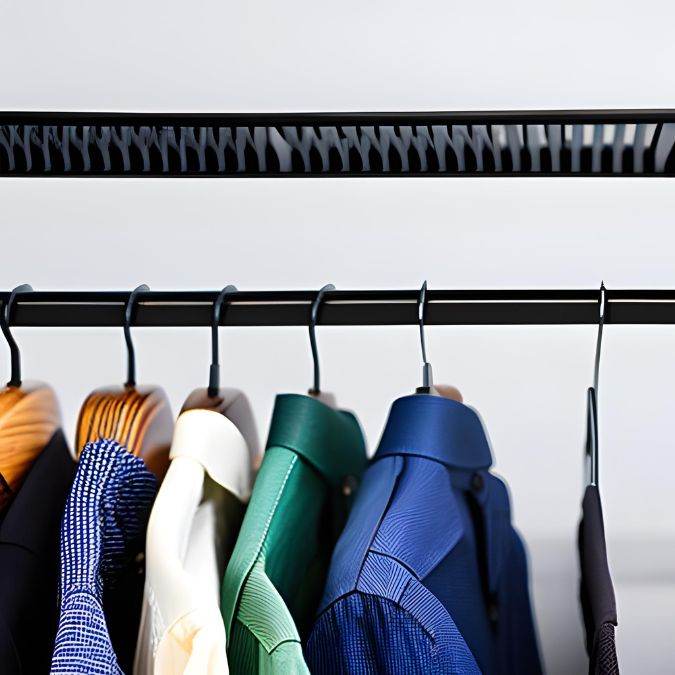
Textile Innovation: Digital printing encourages textile innovation by combining different fabric materials, textures, and printing techniques. This opens up new possibilities for creating visually stunning and technologically advanced textiles.
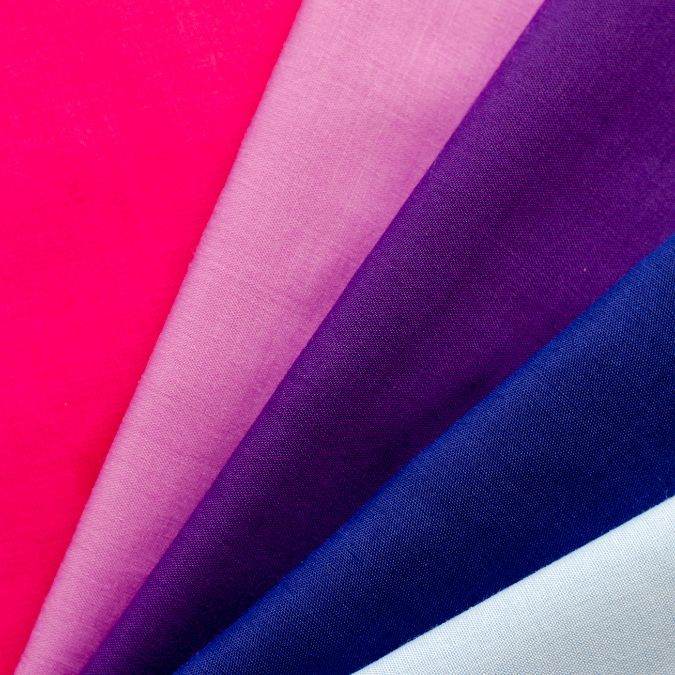
Limited Edition Collections: Limited edition collections in the fashion industry are a popular strategy used by designers to create a sense of exclusivity and uniqueness for their customers. These collections typically feature a limited number of items, often with exclusive prints or designs that are not available in the designer’s regular line. Fashion designers can create limited edition collections with exclusive prints, offering a sense of exclusivity and uniqueness to their customers.
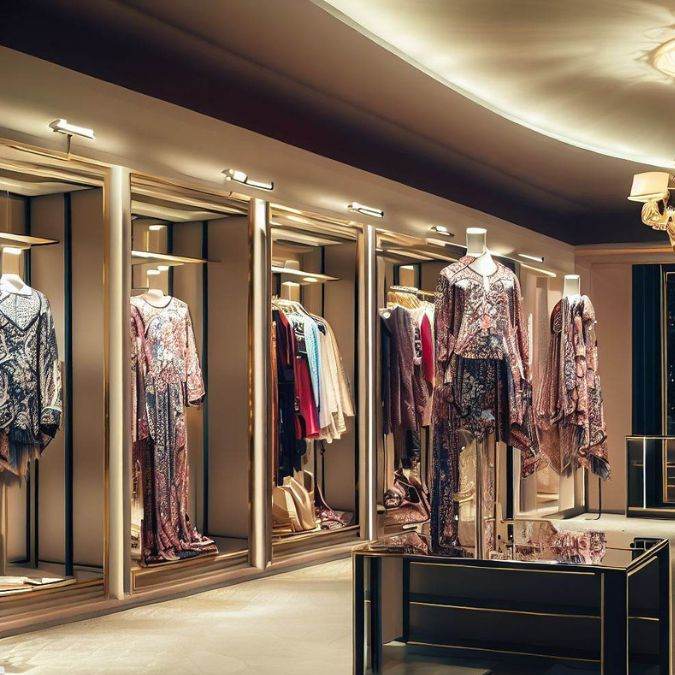
Choosing the Right Fabric for Digital Printing
To achieve the best results in digital printing, it is important to select the appropriate fabric. Factors to consider include:
Fabric Composition: Different fabrics have different ink absorption properties. Natural fibers, such as cotton and silk, are commonly used for digital printing due to their ability to absorb and hold the ink well.
Fabric Weight and Texture: The weight and texture of the fabric can affect the printing process and the final appearance of the print. Lighter fabrics with a smooth texture generally yield better results.
Color Fastness: Fabrics with good color fastness properties ensure that the prints retain their vibrancy and durability even after multiple washes.
Preparing Artwork for Digital Printing
Preparing artwork for digital printing involves optimizing the design files for the best printing results:
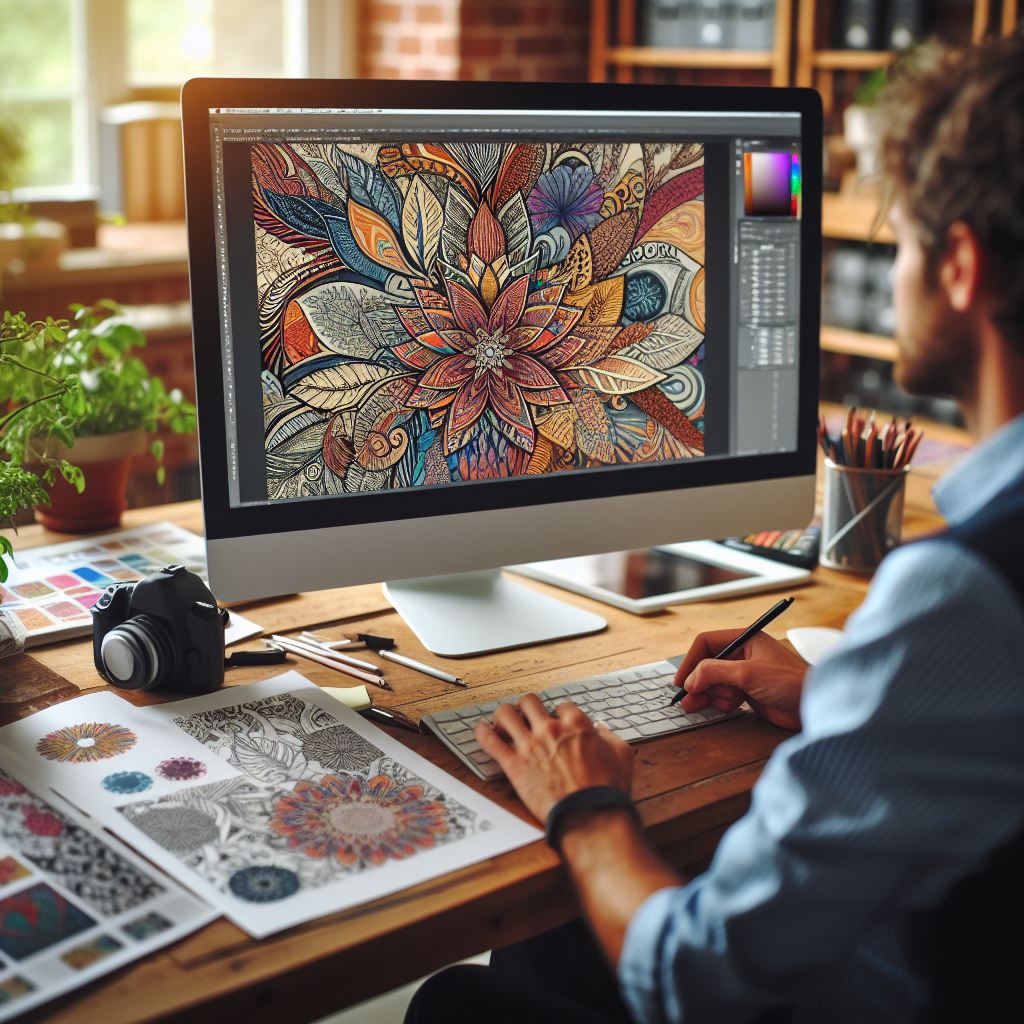
Resolution: Artwork should be created or saved at a high resolution to ensure sharp and clear prints. A resolution of 300 DPI (dots per inch) is commonly recommended for digital printing.
Color Mode: Designs should be created in the CMYK color mode, which is suitable for printing purposes. This ensures accurate color reproduction.
Color Profile: Applying the appropriate color profile, such as Adobe RGB or sRGB, helps maintain color consistency between the design file and the printed fabric.
Maintenance and Care for Digitally Printed Textiles
To prolong the life of digitally printed textiles, proper maintenance and care are essential:
Washing Instructions: Follow the manufacturer’s instructions for washing, including recommended temperature, gentle cycle, and use of mild detergents.
Avoid Bleaching: Avoid using bleach or harsh chemicals that can damage the print or fade the colors.
Sun Protection: Direct exposure to sunlight can cause fading. Whenever possible, protect digitally printed textiles from prolonged sunlight or use UV-protective coatings.
Latest Innovations of Digital Printing on Textiles
Textile innovation through digital printing has revolutionized the fashion industry, and here are a few examples of how it has transformed the field:
- Direct-to-Garment (DTG) Printing: With DTG printing, digital inkjet technology is used to print designs directly onto fabrics, allowing for intricate and detailed patterns, gradients, and vibrant colors to be achieved on garments.
- Sublimation Printing: Sublimation printing involves transferring dye onto fabric through a heat press, resulting in high-quality, permanent prints that are fade-resistant and do not compromise the fabric’s breathability.
- Digital Textile Printing: Digital textile printing enables designers to create complex and unique patterns that can be printed on a wide range of fabrics, including natural fibers like cotton and silk, as well as synthetic materials, with excellent color accuracy and precision.
- Reactive Dye Printing: Reactive dye printing utilizes water-based dyes that chemically bond with the fabric fibers, resulting in prints that are highly durable, soft to the touch, and have excellent colorfastness.
- Discharge Printing: Discharge printing involves applying a color-removing agent to certain areas of a fabric, followed by overprinting with new colors, allowing for intricate and subtle designs with a soft, vintage look.
- Digital Embroidery: Digital embroidery combines traditional embroidery techniques with digital technology, allowing for intricate and detailed designs to be precisely stitched onto fabrics, adding texture and dimension to garments.
These examples demonstrate how digital printing has opened up new possibilities for textile design and production, offering greater flexibility, customization, and creativity in the fashion industry.
Future Trends in Digital Printing on Textiles
The future of digital printing on textiles is filled with exciting prospects and potential advancements that are set to transform the industry. Here are some additional details about these developments:
Sustainable Printing
As the fashion industry becomes increasingly conscious of its environmental impact, there is a growing emphasis on sustainable printing practices. In the future, we can expect the adoption of eco-friendly techniques, such as the use of natural dyes derived from plants, minerals, or even waste materials. Additionally, the development of recyclable and biodegradable inks will contribute to reducing the environmental footprint of digital printing on textiles.
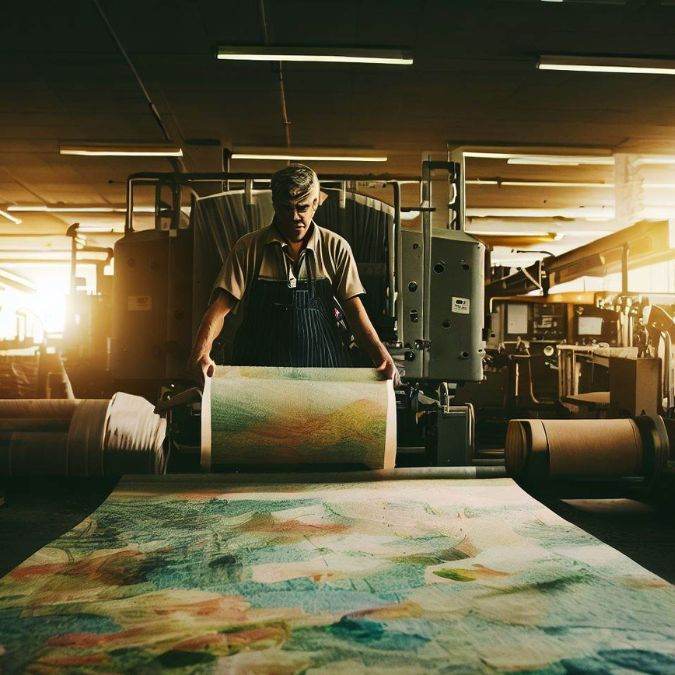
Integration of Technology
The convergence of digital printing with other technologies holds tremendous possibilities for the textile industry. One notable example is the integration of 3D printing into the process. This integration will enable the creation of intricate and unique textile structures, adding texture, depth, and three-dimensional effects to fabrics. Furthermore, the emergence of wearable electronics, such as conductive threads and smart textiles, will provide opportunities to incorporate functional elements into digitally printed textiles, such as integrated sensors, lighting, or even interactive displays.
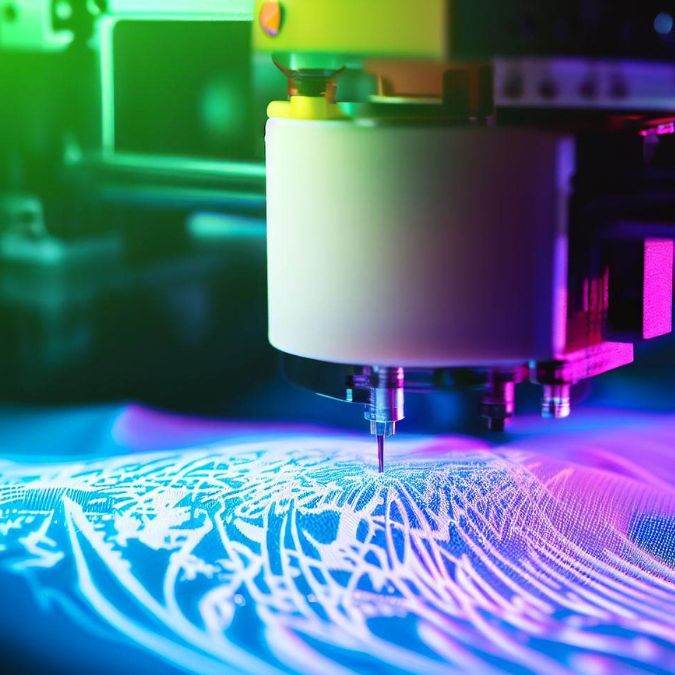
Mass Customization
Digital printing has already paved the way for customization in the fashion industry, and this trend is expected to continue and expand in the future. With further advancements in printing technology, mass customization will become even more accessible and prevalent. Consumers will have the ability to personalize their textiles on demand, allowing for a greater level of individual expression and style. From customized patterns and color combinations to tailored fits, the possibilities for personalized textiles will be virtually limitless.
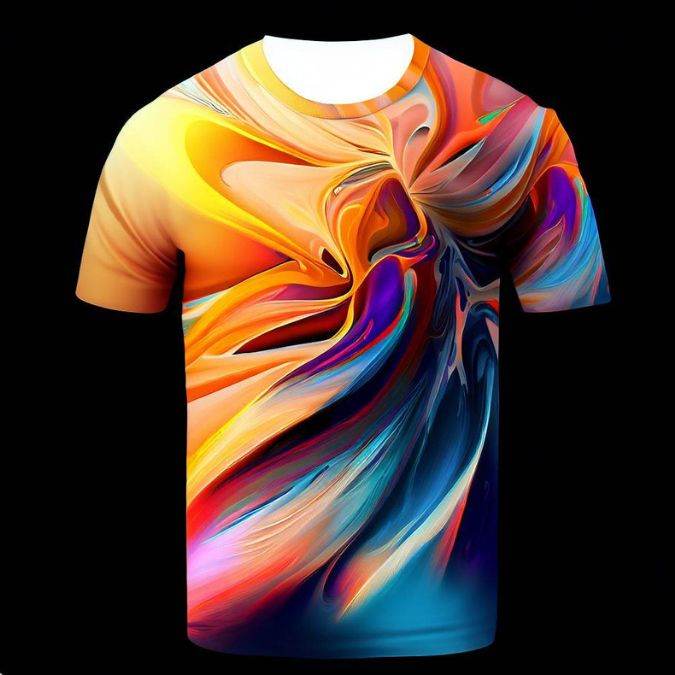
These advancements in sustainable printing, integration of technology, and mass customization will shape the future of digital printing on textiles. As the industry continues to innovate, it will not only cater to evolving consumer demands but also contribute to a more sustainable and personalized fashion landscape.
Conclusion
Digital printing on textiles has revolutionized the fashion and home decor industries, offering unparalleled design possibilities, cost-effectiveness, and high-quality prints. This innovative technique has opened up new avenues for creativity and personalization. As the popularity of digital textile printing continues to grow, it is likely that this technology will become even more widely adopted in the future. This is good news for textile entrepreneurs, as it means that they will have access to a more efficient, cost-effective, and environmentally friendly way to print fabrics.
Frequently Asked Questions (FAQs)
Can digital printing be used on all types of fabrics?
Yes, digital printing can be used on various fabric types, including natural fibers like cotton and silk, as well as synthetic fabrics like polyester.
Are digitally printed textiles durable?
Yes, when properly cared for, digitally printed textiles can be durable and maintain their vibrancy for a long time.
Can I create my own designs for digital printing?
Absolutely! Digital printing allows for customization, so you can create your own unique designs or choose from existing patterns.
Is digital printing more expensive than traditional printing methods?
Digital printing can be more cost-effective, especially for small production runs or customized orders, as it eliminates the need for screens or plates.
What is the future of digital printing on textiles?
The future holds sustainable printing practices, integration of technology, and the potential for mass customization, offering exciting possibilities for the industry.
Digital printing on textiles is a contemporary method of applying designs to fabric surfaces using inkjet technology. It offers benefits such as versatility, customization, reduced waste, and quick turnaround. This technique finds applications in fashion, home decor, advertising, and sportswear. Challenges include color fastness and fabric compatibility, but ongoing developments in technology aim to address these issues. Digital printing is also considered more environmentally friendly than some traditional methods. Overall, it’s a versatile and evolving technology shaping the textile industry.
https://chandnacorporation.com/
Thanks for your informative comment. Stay connected with us for more information like this.
best loggistics courier services